An Ultimate Guide on How to Enhance Workplace Safety with Toolbox Talks
In the United Kingdom, the Health and Safety Executive regulates employers’ responsibilities in managing workplace security. Did you know that the law requires you to make periodic risk assessments? It’s also your duty to brief employees about your findings and clarify how you plan to protect them.
While it’s a no brainer to memorize the “duck-cover-hold” sequence or identify where the emergency exits are, rigorous training is a must to ensure that your team is fully capable of dealing with risks when an emergency arises. When anxiety and panic ensues, how will you keep your employees from forgetting the safety processes and procedures you prescribed?
In this guide, we’ll equip you with the must-knows of safety training via toolbox talks. Quick yet efficient, these briefings will keep your team posted about everything they have to know about workplace safety.
1.0 What is a toolbox talk?
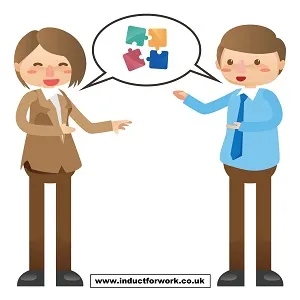
Also known as tailgate or safety briefings, toolbox talks are simply informal meetings held at the beginning of a project. When done correctly, these provide superb opportunities to:
- Reinforce workplace safety basics
- Inform employees and contractors about changes in the working conditions or project site
- Discuss a high-risk accident that recently occurred, and deliver an action plan to make sure it never happens again
While safety briefings are originally tailored for the construction industry, any organization that values the safety of its employees should hold them regularly. As documentation, make sure to jot down the dates when such meetings took place, its agenda, and the attendees.
2.0 What are the safety topics that should be covered in a toolbox talk?
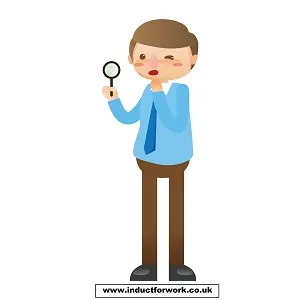
While the core topics that should be covered in a safety briefing may vary from industry to industry, there are a few topics that are applicable across the board.
2.1 Basic Workplace Safety
No matter how many safety training seminars or guidelines you set in place, they are worth nothing if your employees and contractors are not invested in following them. You have to show them why these are important, with emphasis on what could happen if they take no care. In a toolbox talk, you will need to cover basic workplace safety practices such as:
- The need to wear personal protective equipment (PPE) – Whether it’s as simple as putting on earplugs or as complex as setting up a chemical suit, learning how to use PPEs can guarantee your team’s safety against physical harm or hazards inherent in the workplace.
- Why they should never take shortcuts – Workplace policies exist to keep your employees, contractors, and visitors safe in the project site. Each step is designed for a specific purpose, and skipping one procedure alone could mean big trouble! During a toolbox meeting, emphasise the need for your team to use each tool and machine faithfully in accordance with the given instructions.
- The need to keep emergency exits clear – While this seems like common sense, highlight how important it is to keep trolley carts, forklifts, ladders, and other obstructive elements away from emergency exits. Every second counts, so you don’t want a safe route to turn into an obstacle course during emergencies! Moreover, paths leading to emergency equipment shutoffs need to be left clear in case any equipment needs to be powered down urgently.
- Making them aware of their surroundings – Each workplace presents inherent hazards. By being aware of these unavoidable risks and knowing their surroundings, employees and contractors are able to avoid unnecessary workplace injuries. Stress out the need for people to communicate should they identify a potential hazard. You wouldn’t want an exposed live wire left unattended for even just a few hours!
2.2 Office Safety
In an office environment, incidents and injuries such as eye strain and back pain are deemed normal. Hours of sitting in front of a computer desk can really take its toll. Unfortunately, this mindset causes complacency among many workplaces. Set yourself apart and adopt ergonomic changes to prioritize employees’ physical well-being. Your safety briefing should include health and safety tips including:
- How to maintain the right posture
- How to lift and carry items to prevent back injuries
- The need to keep workspaces clutter-free
- Electrical and fire safety practices
2.3 Equipment Safety
Observing the right equipment safety procedures is important not for the operators’ sake, but also for everyone who works in or will visit the building. In your toolbox talks about handing heavy machineries, you’ll want to cover the following:
- Load limits – Make sure operators know how much each machine could only handle. It should also be their second nature to check if the loads are secured with the correct rigging attachments and if all workers are maintaining the prescribed safe distances while loading or unloading is taking place.
- Machine inspections – Before commencing any task, machine operators should perform walk-around inspections with a standard list of parts and components that need checking. This way, they could just place checkmarks for those in good working condition or flag those that seem suspicious. This report should be submitted to the safety department before the machine is powered up.
- Machine maintenance – Remind your workers of safety precautions on machine maintenance, such as never leaving a running machine unattended, discouraging loose clothing to avoid accidentally getting caught by moving parts, and shutting off the equipment first before refueling.
- Blind spots – Highlight how important it is to doublecheck that there’s no one in their blind spots before operating a machine. As an added layer of precaution, workers in locations with heavy equipment should always wear high visibility vests.
- Recommended machine settings – As much as we value productivity, remind operators to follow each equipment’s optimum speed as its manual prescribed.
- Other basic machine operation safety practices and procedures – From mounting the machine properly to fastening their seatbelt, operators must follow all safety practices by the book. Don’t allow anyone to let their guard down! Moreover, they should maintain consistent communication with other workers around them. While two-way radios are the best option, properly trained spotters could also take care of the job.
Since every workplace is unique, make sure the topics in your safety briefing only include those relevant to your team.
2.4 Chemical Safety
When the term “chemical” is mentioned, most people tend to think of scientists working in laboratories. You might ask “why should my administrative office bother about chemical safety?” Heads up, simple bug sprays, cleaning solvents (e.g. bleach, disinfectants, and mildew removers), glues, and fuel are also classified as chemicals. Make sure that your toolbox talk covers how to safely handle them in these scenarios:
- Spill response
- Storeroom safety
- Housekeeping
- Airflow while using chemicals
- Emergency response should someone come into contact with a chemical
The most simple precautionary measure your team could do is to always read the label. Containers usually have Material Safety Data Sheets (MSDSs) to guide anyone before usage.
2.5 Weather-related Safety
Safety briefings need also to consider your area’s weather conditions. In summer, you can advise employees on the need to stay hydrated to prevent heatstroke and skin cancer. Meanwhile during the winter, cover such topics as signs of hypothermia and how to drive safely in the snow.
3.0 Tips for effective communication during toolbox talks
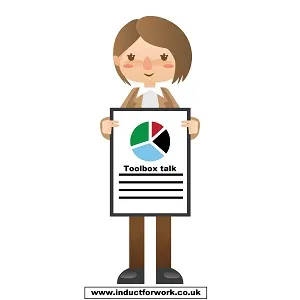
To ensure that your purpose and what the team understood are aligned, keep this checklist of best practices in mind:
- Keep it brief – No matter how complex and important a topic is, your audience’s attention span is highly limited. No one has the patience and capacity to absorb 100 slides in one sitting! Toolbox talks should be brief, so be straight to the point and just put any supporting elaboration in a handout. Avoid repeating the same topic in future meetings and just focus on adding relevant or new content. For maximum comprehension, use short phrases and avoid technical jargon or slang.
- Be relevant – The content of your safety briefings should be relevant to the attendees’ project site or industry. Your job is to make them feel safe, not confused and bored. If employees do not feel that the topics in your safety briefings do not apply to them, they are likely to doze off or lose interest.
- Be mindful of your delivery’s pace – Everyone’s busy or chasing a deadline, but rushing through a safety briefing only defeats its purpose. If you don’t give the closing forum enough time, you might look impatient and uninterested in your team’s questions or opinions. On the other hand, delivering the message too slowly can mean hours of wasted time.
- Maintain a positive attitude – In contrast to incident investigations which are reactive approaches towards workplace safety, safety talks are preventive measures that encourage safe behavior. Therefore, you should focus on what should be done to create a healthy and safe work environment instead of nagging about what has gone wrong in the past.
- Make your safety briefing sessions interactive – one way of making sure that your audience pays attention is by setting your toolbox talks apart from traditional lectures. The secret? Interactive sessions. Demonstrations and role-playing not only give your audience a chance to participate, but also greatly improve data retention. This approach also helps the audience perceive safety briefings as something fun rather than something they have to just tolerate.
- Avoid statistics, tell stories instead – although people the reliability of statistics is unmatched, your team will more likely remember stories. Remember, the ultimate goal of any safety briefing is to keep your employees from forgetting what they’ve been taught. Try to keep the stories you use brief and relevant so they could demonstrate your point clearly.
- Strategic engagement – During your safety briefings, use open questions to evaluate your audience’s level of comprehension. Simply asking basic queries such as “do you understand” prompts your audience to answer “yes” even though they did not understand anything at all.
4.0 How Induct For Work can upgrade your toolbox talks
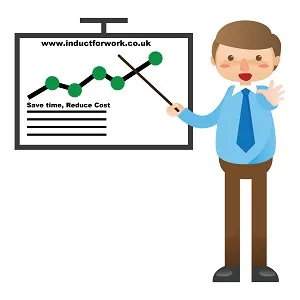
Toolbox talks can take a lot of time and effort from planning to implementation, but Induct for Work can help your HR personnel’s lives easier. Simply put, it is an online safety training platform that could help you effectively deliver your materials in a convenient manner.
Curious about how we’ll make this possible? Let’s walk you through the ways Induct for Work can upgrade your message delivery in toolbox talks:
4.1 It saves you time
Toolbox tools should be short and precise, and delivering your safety briefings online enables you to do exactly that. Through Induct for Work, you can generate individual-centric and engaging safety briefing content in a breeze. Simply send the safety briefing invite to the right people, and they’ll be ready for your project site in no time.
4.2 It allows you to deliver relevant content through templates
Conventional toolbox talks that highly depend on assigned people’s skills and moods pose greater room for errors. In case your HR team messes up, you have to go through the meeting all over again. What’s worse, it might not even be enough to correct miscommunications – putting a lot of employees at risk in the workplace.
Here’s a tip: a superb delivery method is the key to successful safety briefings. To do this, your materials should be tailor-fitted to concerned employees’ needs and job descriptions. Thankfully, Induct for Work provides you with industry-specific templates that include relevant policies, procedures, and work norms. Using templates is an effective tactic to prevent you from getting sidetracked.
4.3 It puts the learners in control
It is a proven fact that adults love to be in control of things, and training processes is no exception. Shifting to online safety briefings provides learners easy access to your materials. Even better, they can work through the module at their own pace and even repeat the parts they found difficult to understand.
4.4 It reduces your operational costs
While traditional methods take concerned employees, department heads, and safety officers out of their regular routine, Induct for Work enables them to access the safety briefing content through their phone or personal computer instead. What’s more, our platform also keeps track of who accessed the safety briefing at what time. This makes compliance with workplace safety and health laws more hassle-free than ever.
4.5 Your toolbox meetings will be more convenient
For optimum results, toolbox talks are supposed to be held regularly. Depending on what industry you belong to, the frequency of meetings could range from daily to weekly. We highly recommend to do so more often if your workplace has a high rotation of employees and contractors. Worry not, since Induct for Work can provide you with customisable modules that are fit for every session. To assist you further in improving your briefings, learners will be able to send feedback or ask questions once you publish an online forum. As a bonus, its tracking functions could even gauge your team’s comprehension levels!
Conclusion
Toolbox talks are a critical part of building a strong safety culture. It’s also a testament of your organisation’s commitment to protect every employee. By hosting periodic safety briefings online, you can potentially save time, effort, money, and most importantly – lives.
Send us any questions or great tips to share? – Contact us here.
Induct for Work – the only system you need to create and manage online inductions in UK.