Hazards frequently identified by safety consultants in the UK often involve tasks such as working at height, handling chemicals, maintaining proper housekeeping, electrical safety, operating forklifts, implementing lockout/tagout procedures and managing confined spaces. Here’s how UK employers can prevent potential tragedies and enhance safety, with a particular emphasis on the importance of induction training.
Working at Height
Working at height is a significant risk in many industries, particularly in construction and maintenance. In the UK, regulations require that all work at height be planned and supervised appropriately. This includes assessing risks, providing proper safety equipment like harnesses and guardrails, and training workers in their use. Regular safety drills and inspections of equipment can further reduce the likelihood of accidents. Induction training ensures that new employees understand these safety protocols from the start, fostering a culture of safety compliance and awareness.
Chemicals
Handling chemicals requires compliance with the Control of Substances Hazardous to Health (COSHH) regulations, which mandate proper labeling, storage and disposal of chemicals to prevent exposure and accidents. Employers must maintain up-to-date Safety Data Sheets for each chemical and train employees on appropriate handling techniques. Implementing secondary containment systems can prevent spills from spreading and emergency response plans should be in place to address potential chemical accidents swiftly and effectively. Induction training is crucial for educating new employees on these critical safety measures, ensuring they are well-prepared to handle hazardous substances safely.
Housekeeping
Good housekeeping is essential to prevent injuries and maintain a safe work environment. This includes regular cleaning schedules, adequate storage solutions, and clear signage to warn of potential hazards. The Health and Safety Executive (HSE) suggests that regular audits can identify housekeeping issues that might not be immediately obvious but could pose significant risks, such as blocked fire exits or cluttered walkways. Induction training helps new employees recognize the importance of maintaining a tidy workplace and understand the protocols for reporting and addressing housekeeping issues.
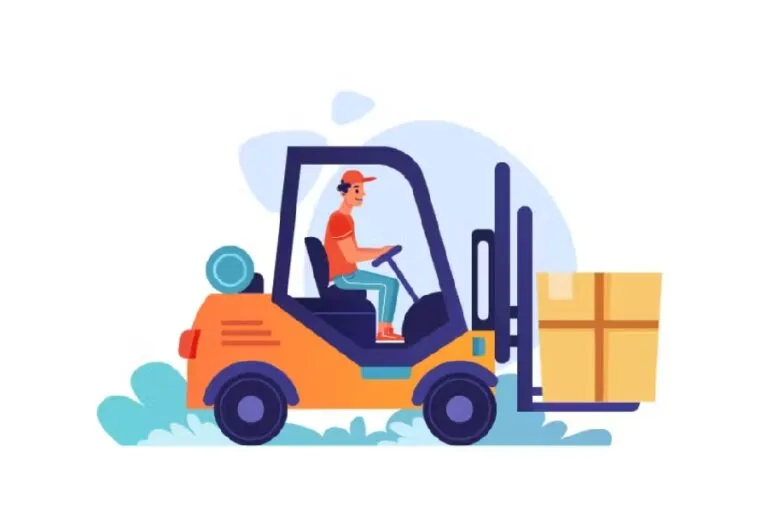
Forklifts
Forklift safety is crucial in warehouse and manufacturing settings. Operators must be trained and hold a current certificate, as required by UK law. Regular maintenance of forklifts is essential to ensure they are safe to use. Traffic management plans should be implemented to keep forklifts separate from pedestrian areas, reducing the risk of collision. Incorporating induction training ensures new employees are aware of these protocols from day one, helping to maintain a safe operational environment.
Lockout/Tagout
Lockout/tagout procedures are critical to prevent machinery from being accidentally energised. Establishing a formal lockout/tagout programme involves training employees on the specific procedures for each type of machinery, including the correct isolation and securing of energy sources. Regular reviews and drills can help ensure that these practices are followed consistently. Induction training can play a vital role in familiarising new employees with these crucial safety procedures, ensuring they understand the importance of following proper lockout/tagout protocols.
Confined Spaces
Work in confined spaces requires strict adherence to safety protocols, including air quality monitoring, emergency preparedness, and specific training for workers. Employers must identify all confined spaces at their sites and develop entry permits that outline the hazards and necessary precautions for each space. Regular training and drills should be conducted to prepare workers for the conditions they might face in confined spaces. Comprehensive induction training should also include confined space safety to ensure all workers understand the risks and procedures.
Leveraging Resources for Safety Compliance
To maintain a safe workplace, it’s crucial for employers to leverage all available resources to understand their safety obligations and address hazardous situations effectively. The Health and Safety Executive (HSE) provides guidance and resources for managing workplace safety, and safety consultants can offer tailored advice and conduct audits to ensure compliance and promote a safety culture.
Implementing comprehensive safety measures, running online inductions on platforms like Induct For Work and maintaining a commitment to continuous improvement can help reduce the incidence of workplace injuries and fatalities. Engaging with professional safety consultants and leveraging resources from organisations such as the HSE can provide additional support and guidance in managing workplace safety effectively.
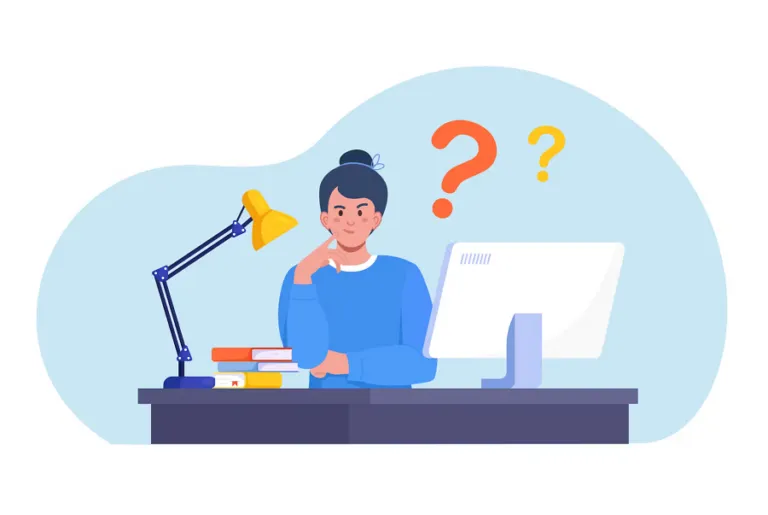
The Importance of Induction Training
Induction training is vital for integrating new employees into the safety culture of an organisation. It ensures that all new hires understand the specific safety protocols and regulations relevant to their roles from the outset. Induction training covers the critical safety practices discussed, such as handling chemicals, working at height, operating forklifts, and managing confined spaces.
By providing thorough induction training, employers can:
- Ensure Compliance: New employees learn about legal and regulatory requirements, helping the organisation remain compliant with safety standards.
- Reduce Accidents: Well-informed employees are less likely to engage in unsafe practices, reducing the risk of accidents and injuries.
- Promote a Safety Culture: Induction training fosters a culture of safety awareness and responsibility, encouraging employees to prioritise safety in their daily tasks.
Final Words
By addressing key areas such as working at height, handling chemicals, housekeeping, electrical safety, forklift operation, lockout/tagout procedures and managing confined spaces, employers in the UK can significantly enhance workplace safety. Regular training, compliance with regulations and proactive risk management are essential in creating a safe working environment.
Employers should remain vigilant and committed to continuous improvement in their safety practices. Utilising available resources, conducting regular safety audits and ensuring thorough induction training can help mitigate risks and protect the well-being of their workforce. By fostering a strong safety culture, workplaces can not only comply with regulations but also ensure a safe and productive environment for all employees.